Frequently Asked Questions ( FAQ ) About Log and Timber Homes
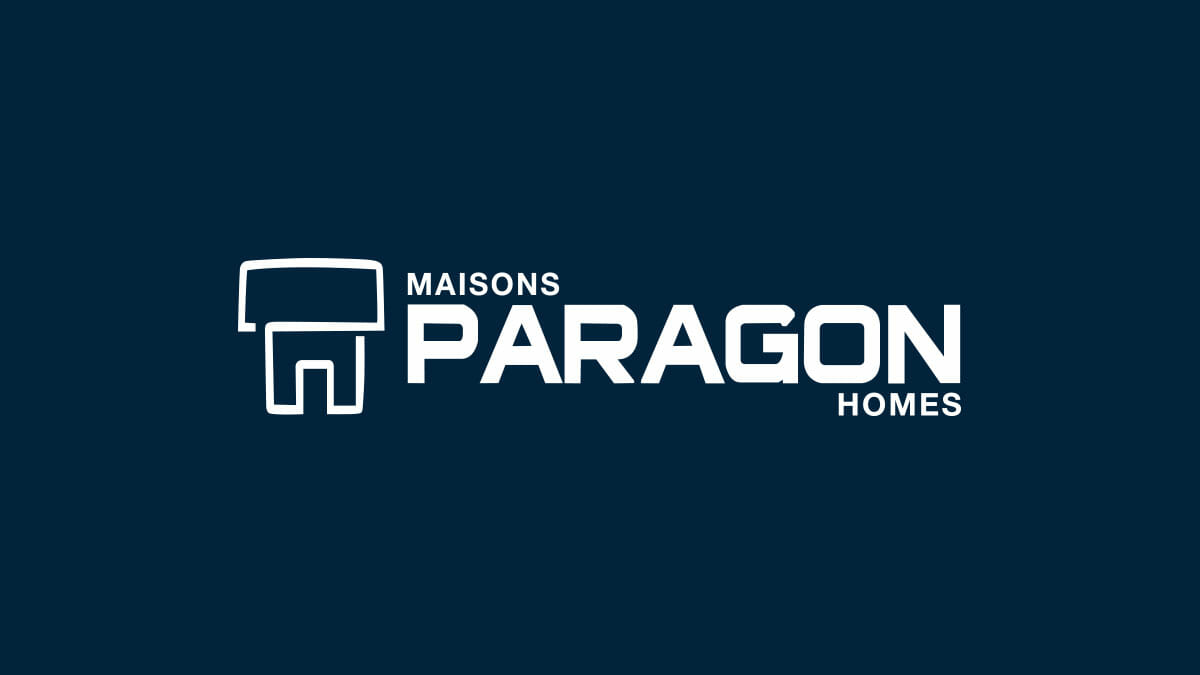
We get many questions and requests about log homes, log construction, timber framing and what’s the difference between hybrid timber and true timber frame construction. We have compiled a list of the most frequently asked questions below.
How Energy Efficient is a Log Home?
A log or timber frame home can be as energy efficient as a conventional home, provided that the home is properly constructed to best practices. While the apparent R value of a solid wood home may appear less on paper – for example, an 8 inch wall yields a value of R-18, solid wood walls create a battery effect, collecting heat during the day and slowly releasing it at night, due to their thermal mass. In ALL homes, regardless of the framing system, the key elements to consider relate to making the home airtight, and using best practices in construction.
What is included in your log home and timber frame home packages?
Our log home kits are quite complete and include everything you will need to build the structure for your home including the floor and roof systems, doors and windows, perimeter walls and interior walls, gables, soffits and fascias. We encourage you to ask us questions and contact us so you can perform accurate comparisons when budgeting for your new log or timber frame home. Have a look at our Material list.
What must I add to complete my log or timber frame home?
To complete the construction of your log or timber frame home you will need to add the following elements:
- Foundation, well, septic and excavation
- Interior mechanicals: plumbing, heating and ventilation systems and fixtures
- Electrical systems and fixtures
- Floor finishes such as carpet, ceramic or wood
- Kitchen and bath cabinets
Can I change the components of my log home/timber home package?
Absolutely. We can accommodate most every need that you may have for your log or timber frame kit. This includes options such as decks and porches, substitutions such as plywood flooring, changes to windows and doors, roof systems, floor square footage adjustments, garages, changes to partitions, and so on.
What if I have my own design or design ideas for my log or timber home?
You can bring us your own plans or ideas and we can work from there to build you a log home kit. We can even design a log home or timber frame home for you from scratch using a process that identifies your needs and budget.
Is Buying or Building a Log Home or Timer Frame Home More Expensive?
Yes it is, as these types of homes are much more complex to assemble. Specialized trades are required as both log and timber frame homes have very particular requirements related to framing, window and doors installation, electricals, mechanicals and other systems.
How do I select trades to build my log/timber home?
First and foremost, the trades you select should have knowledge of log and timber construction and experience in doing so. This applies to:
- mechanical companies and trades such as plumbing, heating and ventilation contractors
- electricians
- framers and building crews
- window and door installers
- insulation contractors
Building a log or timber home is different. The key is to select good, highly experienced trades. If you are in the region, we can of of course handle all of this for you using our unique construction project management system.
Are log home corners built on-site or at the factory?
All log corners are cut on-site by the builder. You do not have to be confined to any particular type of corner style. In most instances, you would pay a hefty premium for particular corner treatments when buying a pre-engineered kit home. By leaving log corner cutting on-site, you can save money and get the exact corner detail that you want.
What wood species do you offer for log and timber homes?
We use eastern white pine exclusively. It is renowned as a strong, durable and economical wood species. It is easily worked (for corner details for example), has a uniform texture and features low shrinkage. It is also a fast-growing tree that is widely used in landscaping and reforestation efforts. We do not use standing dead wood or inferior grade trunks and no trees with insect infestations. All logs are dried naturally. We also offer cedar as a special option.
Do you kiln-dry logs and timbers?
No. Some manufacturers opt for kiln-drying when the lumber used is standing dead wood or low-grade lumber in order to kill insects and reduce moisture content. But the process will generally only act on the first inch or so of the log. And once the log exits the kiln, it will re-acquire its moisture once in the environment. We believe kiln-drying may be more appropriate for small dimensional lumber (2X4’s for example) and not for large solid logs.
What is the difference between log and timber framing?
In an engineered square log structure, logs come in small 8 foot sections and are splined together to make up the log wall system. Logs are stacked horizontally, one on top of each other, to make up a solid wall. In some instances logs may be full length, but this is more expensive and more difficult to handle and erect. A timber frame home is an open framework of large structural (load-bearing) timbers that are exposed inside the house and become an integral part of the home’s look and feel. In a timber hybrid, the timbers are reserved for the main living area/great room, whereas the bedrooms and “wings” of the home are constructed using “stick-framing” to keep costs down. Joinery between timbers may also be steel in order to reduce costs.
What is the difference between true timber frame and post and beam construction?
Actually, the terms are interchanged somewhat liberally. In general, a true timber frame construction uses solid wood timbers throughout the wall and roof system, whereas a post and beam can use a mix of solid timbers, standard dimensional lumber and laminated or structurally engineered wood products like glulam and paralam beams.
What’s the Difference between a hybrid and a true timber frame home?
A hybrid timber home is an interesting alternative for those who love the look of a timber frame home but that are concerned about the costs of timber framing. In a hybrid design, a conventionally erected shell is designed using conventional lumber, after which timbers are then grafted onto the structure. The add-on timbers are still substantial in size, but, unlike a true timber frame home, they are not load-bearing, which provides many cost and visual benefits:
- you get to decide how much timber will be exposed throughout the home
- you get to set the upper limit for timber sizes to save on costs
- you can modify the look and feel of the timber design without being worried about structural details
- you can reduce the timber spacing to your liking
- custom joinery (e.g., tongue and fork, blind mortises, etc…) is eliminated
- conventional framing crews can be used to frame your home
- you can literally “add” timber elements over time
- A hybrid gives you the big timber look you want, without the expense.
Is Timber Framing more expensive than log?
Yes. Large timbers are much more expensive than smaller timbers and, unlike a solid log wall, each timber is a stand-alone structural, load-bearing element. A timber frame kit may include timbers that are 8X10, 8X12 and much larger. By comparison, a basic log kit uses a 6X8 log for its walls. In general, trees that can yield an 8” log are much more plentiful. So while there is generally less timber in a timber frame home, the timbers are much more expensive.
What type of timbers are used in a hybrid timber frame home, and how are they joined?
As a general rule, timbers come in two types – a solid 6X8 pine timber or, a machined hollow timber, which is available in any size, but which is usually 8X8 pine Solid timbers give you the rustic charm of a timber home, complete with checks and cracks, whereas hollow timbers generally do not check and crack as they are engineered and machined to tight tolerances using milled pine lumber. Joinery for a hybrid is quite flexible, but usually consists of mitred joints and/or metal braces to keep costs down.